Upscaled, Robotic Coreless Filament Winding Methods For Lightweight Building Elements For Architecture
Starting in the 1940s, advances in the chemical industry and composite materials such as Fiber Reinforced Polymers have revolutionized manufacturing enabling new lightweight – high strength applications in the aerospace, automotive, and consumer goods industries. However, composites failed to significantly impact the building construction industry due to its poor digitalization and low integration of design and engineering methods. Nevertheless, these shortcomings can be mitigated through construction-specific design, fabrication methods, and building regulations for new composite structures.
Especially, lightweight construction has yet to capitalize on the high strength-to-weight ratio afforded by composite materials such as Glass or Carbon Fiber Reinforced Polymers and thus shape its contribution to contemporary high-performance, lightweight architecture. However, 21st Century advances in digital design methods in conjunction with newly available hardware and control systems allow for automated fabrication approaches to re-imagine established fabrication methods such as Filament Winding (FW).
Through his Doctoral thesis, Upscaled, Robotic Coreless Filament Winding Methods For Lightweight Building Elements For Architecture, Serban Bodea presents novel upscaling and automation strategies for Coreless Filament Winding (CFW), which is an adaptation of FW to construction applications. CFW is a fabrication method that relies on the anisotropic mechanical properties of free-spanning fibers wound around supports in space to create efficient load-bearing structures without requiring molds or dies. These strategies are supported by a state-of-the-art review focused on the technological requirements for robotic coreless filament winding in construction applications. The investigation identified limited scalability of the fabrication method and insufficient process automation as research gaps in the academic investigation for construction composites. The thesis demonstrates that existing prefabrication methods of Robotic Coreless Filament Winding (RCFW) can be successfully upscaled and utilized for large-scale, long-span loadbearing structures. Furthermore, the thesis presents an approach to advance existing process-monitoring and quality-control methods, named Cyber-Physical RCFW (CPRCFW). The two objectives are investigated through two representative tasks: (1) verifying the RCFW method’s scalability and its industrialization potential, and (2) the development of a CPRCFW method for quality control, integrating winding process automation, process monitoring, data acquisition, and analysis. Each objective is demonstrated through the research and development of hardware, consisting of fabrication setups and tooling and software, comprising CAD-implemented industrial robot motion planning and control algorithms. The objectives are verified through large-scale demonstrators at the component and at the building scale, illustrating how the research findings are conducive to RCFW becoming a valid alternative to industry-verified technologies in composite construction applications.
Scientific Development
Serban Bodea
Supervisor and first examiner
Prof. Achim Menges, Institute for Computational Design and Construction (ICD)
Second examiner
Prof. Jan Knippers, Institute of Building Structures and Structural Design (ITKE)
PROJECT FUNDING
Baden Württemberg Stiftung, Ausschreibung Innovation durch Additive Fertigung
RELATED PUBLICATIONS
S. Bodea, C. Zechmeister, N. Dambrosio, M. Dörstelmann, A. Menges: 2021. Robotic coreless filament winding for hyperboloid tubular composite components in construction. Automation in Construction 126, 103649. https://doi.org/10.1016/j.autcon.2021.103649
Bodea S., Mindermann P., Gresser T., Menges A.: 2021, Additive Manufacturing of Large Coreless Filament Wound Composite Elements for Building Construction, 3D Pinting and Additive Manufacturing, Mary Ann Liebert, Inc. Publishers. https://doi.org/10.1089/3dp.2020.0346
Mindermann P., Bodea S., Menges A., Gresser T.: 2021, Development of an Impregnation End-Effector with FiberTension Monitoring for Robotic Coreless Filament Winding, Processes, Molecular Diversity Preservation International(MDPI). https://doi.org/10.3390/pr9050806
Bodea, S., Dambrosio, N., Zechmeister, C., Gil Perez, M., Koslowski, V. Rongen, B., Doerstelmann, M., Kyjanek, O., Knippers, J., Menges, A.: 2020, BUGA Fibre Pavilion: Towards Robotically-Fabricated Composite Building Structures, in Burry, J., Sabin, J., Sheil, B., Skavara, M., (eds.), Fabricate 2020: Making Resilient Architecture, UCL Press, London, pp. 234-243. (ISBN: 9781787358119)
Dambrosio, N., Zechmeister, C., Bodea, S., Koslowski, V., Gil-Pérez, M., Rongen, B., Knippers, J., Menges, A.: 2019, Towards an architectural application of novel fiber composite building systems – The BUGA Fibre Pavilion. in ACADIA – Ubiquity and Autonomy [Proceedings of the ACADIA Conference 2019]. The University of Texas, Austin. (ISBN 978-0-578-59179-7)
Zechmeister, C., Bodea, S., Dambrosio, N., Menges, A.: 2020, Design for Long-Span Core-Less Wound, Structural Composite Building Elements, in Gengnagel, C., Baverel, O., Burry, J., Ramsgaard Thomsen, M., Weinzierl, S. (Eds.), Impact: Design With All Senses [Proceedings of the Design Modelling Symposium 2019], Springer International Publishing, Cham, pp. 401-415. https://doi.org/10.1007/978-3-030-29829-6_32
Contact Information
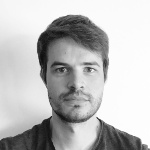
Serban Bodea
Dr.-Ing.Doctoral Candidate