Autonomous Assembly
Artificial Intelligence Methods for Collective Robotic Construction
Context
Robotic and automation technologies are making a significant impact across industrial sectors. From self-driving cars (transportation) to dark factories (manufacturing), and from drone seeding (agriculture) to autonomous container ships (infrastructure), industries across the board are benefiting from the increased speed, precision, and efficiency that such automation affords. Although robotic processes have also gained more use in the AEC industry (architecture, engineering, and construction), these have primarily focused on adapting manufacturing technologies (like robot arms) for automating off- and on-site prefabrication of building elements, while the automation of on-site assembly remains a challenge.
Theory
Drawing principles from natural builders, like termites and weaver ants, Collective Robotic Construction (CRC) has emerged as a promising theory to address this automation gap. Within the CRC framework robots are (1) mobile, meaning they can move around and usually climb on the structure they are building, (2) distributed, meaning they can execute tasks in parallel, and (3) collaborative, meaning they can perform increasingly harder tasks by cooperating with more agents. These (and more) features directly contrast with machinery in traditional construction sites like cranes, tractors, and gantries whose limited workspaces, human-centered topologies, linear logics, and monolithic proportions prevent scalability and autonomy. The introduction of CRC into architectural practice would have wide repercussions, from influencing design methods to enabling novel and faster ways for architecture to consider and respond to societal demands.
Problem Definition
While CRC offers theoretical solutions to the automation of on-site assembly, implementations are still in their infancy because scalable decision-making and motion planning approaches to such assembly problems are missing. This is the case because they involve a tight interplay between robot, material, planning, and structure thus requiring a co-design (multi-objective and interdisciplinary) approach to be solved. Furthermore, the theoretical ideas proposed by CRC (mobile, distributed, collaborative, etc.) are inherently coupled to various challenges, such as the intractability of solving geometric rearrangement problems in high dimensional solution spaces, the difficulty of designing controllers that can react to non-linear material behavior, and the flexibility required to schedule tasks while accounting for multiple, often conflicting, constraints and execution times.
Research Question
This thesis hypothesizes that recent advancements in AI can help us in solving these problems and thus enable CRC technologies to fill the automation gap in the AEC industry. This will make the industry more adept at handling today's problems (e.g. increased demand for housing due to mass migrations, meeting sustainability goals set by international organizations, etc.) that require faster, more sustainable, and more efficient on-site assembly. Therefore the research question has two parts: How can we employ AI methods to realize the various theoretical ideas of CRC, and what implications does this have for AEC?
Methodology
This question will be tackled in four work packages according to the following methodology: (1) a theoretical CRC idea is identified based on its relevance to current industry demands; (2) the idea is paired with suitable AI methods; (3) the pair is implemented using a case study CRC system; and (4) the system is compared to other platforms in terms of throughput, scalability metrics, and its ability to address the aforementioned demands. This is intentionally a very pragmatic methodology, as one of the goals of this dissertation is to prove that the technology is ready to go beyond laboratory experiments and have a real-world impact, and thus should be developed with both practicality and societal impact in mind (Where can we use this? How can it scale? Who has access to it? What level of expertise is required? etc.).
Work Plan
In the first work package (WP1), we show how we can use Reinforcement Learning (RL) to teach CRC robots how to manipulate unpredictable and irregular materials, thus increasing the range of materials we can build with. In the second (WP2), we demonstrate how Task Graph Scheduling (TGS) can be used to allocate tasks to various agents in such a way that the schedule can be executed in parallel, thus exponentially reducing construction time, and making the system capable of reorganizing itself in case of failures, as the schedule can be iteratively recomputed based on real-time execution results. Inspired by the load transport behavior of ants, the third work package (WP3) shows how Logic-Geometric Programming (LGP) can be leveraged as a coordination mechanism for cooperatively transporting building elements that are beyond the capabilities of a single robotic agent to manipulate. Then we show how this loosens the restriction of material size and weight that is often placed on CRC systems. This is particularly beneficial when working with materials that rely on the continuity of cellulose fibers for structural properties, like wood and bamboo. Finally, in the fourth work package (WP4) we build on the work of the Learning and Intelligent Systems Lab where a robot arm was co-optimized with a manufacturing task. We take this idea one step further and explore genetic programming (GP) as a method to co-design the geometries and kinematics of robots and materials in CRC systems and use the task and motion planning algorithms developed in the previous three work packages as testing grounds for this co-optimization.
Expected Results
From a technical perspective, the hardware and software technology developed from this dissertation will form the infrastructure and backbone for ICDs emerging CRC group, opening the door to many opportunities and further research into the area. From a conceptual perspective, this dissertation expects that the combination of AI and CRC has the potential to revolutionize not only how we assemble architectural structures but also how we think about such structures and processes, thus inducing a much-needed Copernican turn in the conceptual model of robotics in construction.
PROJECT TEAM
ICD Institute for Computational Design and Construction, University of Stuttgart
Nicolas Kubail Kalousdian, Prof. A. Menges
PROJECT FUNDING
Cyber Valley Research Consortium (CyVy-RF-2021-18)
BBSR Zukunft Bau (SWD-10.08.18.7-20.48)
Cluster of Excellence Integrative Computational Design and Construction for Architecture (IntCDC) (EXC 2120/1 RP 19)
RELATED PUBLICATIONS
Kalousdian, N. K., Łochnicki, G., Hartmann, V. N., Leder, S., Oguz, O. S., Menges, A., Toussaint, M.: 2022, Learning Robotic Manipulation of Natural Materials With Variable Properties for Construction Tasks. IEEE Robotics and Automation Letters 7 (2), 5749-5756. (DOI: 10.1109/LRA.2022.3159288)
Contact Information
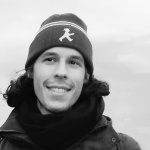
Nicolas Kubail Kalousdian
M.Sc.Research Associate